Summary
Chapter 7 of ISO 9001:2015 emphasizes the importance of support from adequate resources to effectively establish, implement, maintain and continuously improve the quality management system (QMS). This support includes personnel, infrastructure, working environment and the monitoring and measurement of resources. Organizational knowledge also plays a decisive role in the success of the QMS. It is important that sufficient staff and resources are made available so that high-quality work and products can be created. Careful planning and provision of these resources by the management are essential. The standard also requires effective utilisation of these resources in order to achieve the set objectives and continuously improve quality.
Standard section 7.1 Resources
7.1.1 General information
The organization must identify and provide the necessary internal and external resources for the introduction, maintenance and continuous improvement of the QM system.
What does that mean in concrete terms?
ISO 9001:2015 aims to prevent failure due to a lack of resources. The standard requires that companies provide sufficient personnel and resources to ensure quality workmanship and the creation of good products and services. In addition, sufficient resources must be available to operate and improve the QMS processes themselves.
How can this be implemented in practice?
Practical implementation can be achieved by integrating resource planning into project management, especially when it comes to major changes or new challenges. In smaller companies, the consideration of necessary investments often takes place in the mind of the entrepreneur, but it makes sense to make these considerations transparent in the management review and to plan and implement them accordingly. In both large and small companies, it is a challenge to effectively utilize the financial means to procure resources and to balance the needs of the various departments and processes.
This updated summary and the first subtopic are intended to give readers a deeper insight into the requirements of Chapter 7 of ISO 9001:2015 and provide practical tips for implementation.
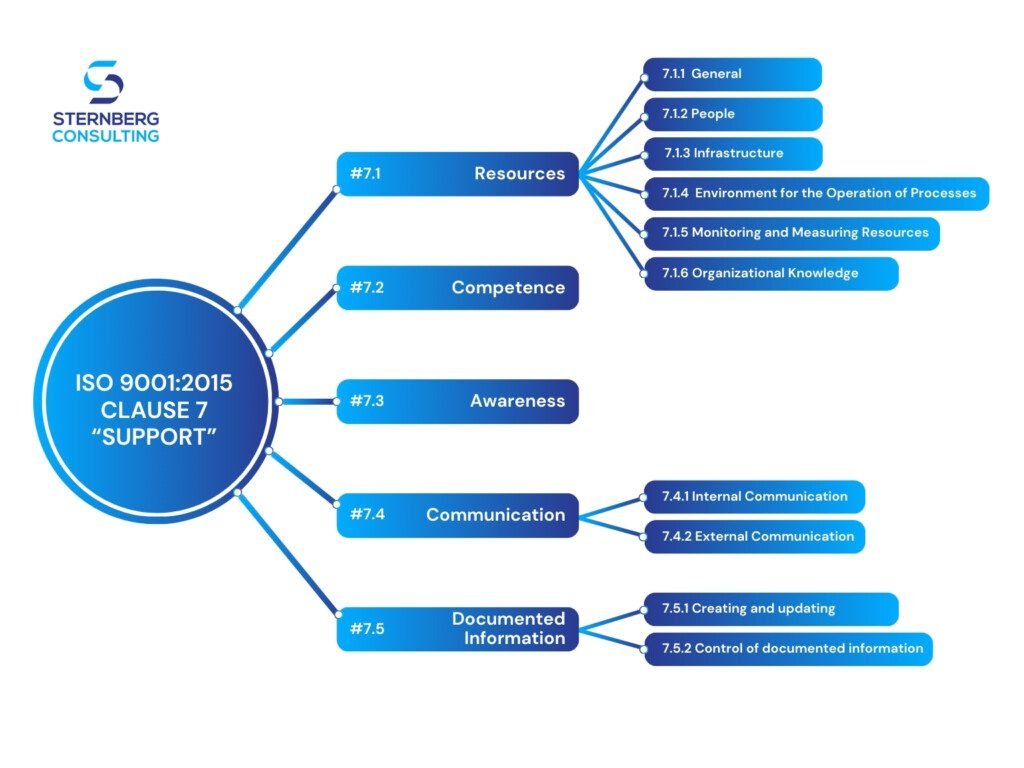
ISO 90012015 CLAUSE 7 “SUPPORT”
Chapter 7.1.2 People
Summary
This section of ISO 9001:2015 is about the heart of every organization – the employees. It emphasizes how crucial it is that sufficient qualified personnel are available to achieve the quality objectives and operate an effective quality management system (QMS). The focus is on the provision and management of human resources to ensure that the competence, awareness and working conditions of employees support the implementation and maintenance of the QMS.
What does that mean in concrete terms?
In concrete terms, this means that companies must actively ensure that their staff are not only available in sufficient numbers but also have the necessary skills, knowledge and experience to carry out their work in accordance with quality requirements. It is about promoting a culture of quality awareness and creating a working environment that empowers employees to contribute to continuous improvement.
How can this be implemented in practice?
The practical realisation of this principle can be achieved through a series of steps:
- Competence analysis: Firstly, the company should define the competences required for each role within the QMS. This analysis can focus on education, professional qualifications, experience and additional skills.
- Training and development: Based on the skills analysis, training programmes should be developed to close existing skills gaps. These programmes can be carried out internally or externally and should include an evaluation of the success of the training.
- Promoting awareness: All employees should be regularly informed about the company’s quality objectives, their role in the QMS and the importance of their work for quality results. This can take the form of regular meetings, newsletters or special information events.
- Creating a supportive work environment: Management must ensure that the work environment (including physical, technological and social conditions) supports all employees in carrying out their tasks effectively and efficiently.
- Feedback and communication: An effective feedback system that allows employees to suggest ideas for improvement and raise concerns about quality should be established.
By focussing on the people who are involved in the creation and delivery of products and services on a daily basis, a company strengthens its quality management system and promotes a culture of continuous improvement.
Chapter: 7.1.3 Infrastructure
Summary
Section 7.1.3 of ISO 9001:2015 addresses an organisation’s infrastructure as a key component required to deliver compliant products and services. Infrastructure refers to the entirety of all buildings, tools, technologies and any equipment required for operations. This section emphasises the importance of identifying, providing and maintaining physical and technological resources in order to ensure process efficiency and increase product quality.
What does that mean in concrete terms?
In concrete terms, this means that companies must make targeted investments in their facilities, equipment and support services in order to ensure efficient production and service provision. It is not just about the initial provision, but also about the ongoing maintenance and adaptation of the infrastructure to the changing requirements of the market and the internal process environment.
How can this be implemented in practice?
The practical implementation with regard to the infrastructure can include the following steps:
Assessment of the requirements: A thorough assessment of the specific infrastructure needs for all critical processes is required at the outset. This includes identifying the required buildings, equipment, technologies and support services.
Planning and deployment: Based on the assessment, detailed plans should be developed for the procurement, development and commissioning of the required infrastructure. This should also include the spatial arrangement in order to support optimal workflows.
Maintenance and servicing: A regular maintenance and servicing programme is essential to maintain operational capability and safety. This programme should include preventative measures and routines to minimise breakdowns and maximise equipment life.
Monitoring and adjustment: The effectiveness of the infrastructure must be continuously monitored to ensure that it meets the needs of the organisation. Adjustments should be made to respond to changes in the production process, new technologies or growth opportunities.
Documentation and records: It is important to keep detailed records of the infrastructure components, their condition, maintenance history and all relevant safety checks. This documentation serves as the basis for continuous improvement and proof of compliance.
By focussing specifically on infrastructure, companies can create a solid basis for the quality of their products and services and at the same time improve the efficiency and effectiveness of their operational processes.
Chapter: 7.1.4 Process environment
Summary
A suitable environment for the execution of processes is a crucial aspect of quality management. A well-designed working environment contributes significantly to product quality and employee satisfaction. With this in mind, section 7.1.4 of ISO 9001:2015 deals with the need to create a conducive working atmosphere that addresses both the physical and psychosocial needs of employees.
What does that mean in concrete terms?
In concrete terms, this means that the company must create a working environment characterised by sufficient physical space, suitable equipment and a supportive atmosphere. Safety and flexibility are also key factors that influence the well-being of employees and their ability to perform high-quality work.
Factor | Meaning |
---|---|
Physical space | Ample space for operation, reducing clutter and potential for errors. |
Equipment | Equipment is properly maintained and appropriate for the task at hand. |
Atmosphere | A positive, supportive atmosphere that promotes quality and efficiency. |
Security | Ensuring health and safety regulations are followed to protect employees. |
How can this be implemented in practice?
Evaluation of working conditions: Review and adjust physical workplace conditions to ensure a clear and safe working environment.
Maintenance management: Regular maintenance of the equipment to ensure its suitability and functionality.
Developing the work culture: Creating a culture that encourages and supports employees to commit to quality and efficiency.
Safety measures: Implementation of and compliance with health and safety regulations to protect employees.
Promoting flexibility: developing systems and processes that can be adapted to change and innovation to enable continuous improvement and adaptability.
These steps help to create a working environment that not only improves quality and productivity, but also promotes greater employee satisfaction and contributes to the overall quality management strategy.
Chapter: 7.1.5 Resources for monitoring and measurement
Summary
Section 7.1.5 of ISO 9001:2015 sets out the need to ensure appropriate measurement resources for the verification of product and service quality.
What does that mean in concrete terms?
This means that companies must ensure that their measuring instruments are precise and reliable and that the measurement results are traceable.
How can this be implemented in practice?
- Procurement of measuring equipment: When selecting measuring equipment, care must be taken to ensure that its measuring accuracy meets the requirements of the specific measuring tasks. They must also be suitable for the intended measuring range and the environmental conditions in which they are used.
- Calibration strategy: The calibration plan must take into account the frequency of calibration based on the frequency of use and the importance of the measurement for the quality check. Instruments that perform critical measurements may require more frequent calibrations.
- Maintenance procedures: A clear maintenance procedure for measuring instruments must be established to ensure that they are always in good working order. This includes cleaning, regular inspection and, if necessary, repair or replacement.
- Records of calibration and maintenance: Complete records must be kept of every calibration and maintenance carried out. This includes the date, the person carrying out the calibration, the standards used and the results of the calibration.
- Procedure for non-compliant measuring equipment: In the event that measuring equipment is identified as non-compliant, companies must have a procedure in place that describes how to deal with the instrument and the measurement results concerned.
- Labelling of measuring equipment: All measuring equipment must be clearly labelled to indicate the current calibration status and to document when and by whom the last calibration was carried out.
These structured steps ensure that the measuring equipment has the required accuracy and reliability and that the measurement results serve as a reliable basis for quality decisions.
Chapter: 7.1.6 Knowledge of the organisation
Summary
Section 7.1.6 of ISO 9001:2015 deals with the importance of organisational knowledge for the maintenance and continuous improvement of a quality management system. Companies are required to record relevant knowledge, keep it up to date and make it accessible for quality assurance purposes.
What does that mean in concrete terms?
In concrete terms, this requires companies to identify, manage and protect the knowledge that is essential to their business processes. This includes not only explicit knowledge that can be documented, but also implicit knowledge that exists in the minds of employees.
How can this be implemented in practice?
- Knowledge capture: Identification of internal and external knowledge that is important for the execution of processes. This can include customer feedback, information from suppliers, knowledge from previous projects and employee experience.
- Knowledge management: Establishment of a system or process to store and update the collected knowledge and make it accessible to all relevant employees.
- Knowledge retention: Ensuring that important knowledge is retained in the company when employees change. This can be done through documentation, training or mentoring programmes.
- Knowledge dissemination: Promoting the exchange of knowledge within the company through workshops, regular meetings and collaborative platforms.
- Assessment of knowledge requirements: Regular review of existing knowledge in relation to new requirements, changes in the market or in technologies and, if necessary, adjustment of the knowledge base.
- Protection of knowledge: Taking measures to protect confidential knowledge and intellectual property, including patents and copyrights.
These measures ensure that the company has a solid foundation of organizational knowledge, which is essential for long-term success and competitiveness.
7.1.6 Knowledge of the organization
Summary
Section 7.1.6 of ISO 9001:2015 aims to ensure that employees always have access to the necessary and up-to-date information to carry out their work in a quality-compliant manner.
What does that mean in concrete terms?
It means that organizations must ensure that relevant knowledge – be it technical expertise or specific process knowledge – is available and up-to-date for employees. This knowledge includes both internal experience and external expertise.
How can this be implemented in practice?
- Knowledge retention and transfer: Actively gathering knowledge through internal training, workshops or by forming teams in which experienced employees pass on their knowledge to less experienced colleagues.
- Documentation of expertise: Recording knowledge in the form of process descriptions, work instructions, guidelines and technical documentation that is made easily accessible.
- Development of knowledge databases: Use of IT systems such as company wikis to record solutions to specific problems and facilitate the reuse of knowledge.
- Updating external knowledge: Ensuring that norms, regulations and technical standards that are relevant to the company are always kept up to date.
- Knowledge updater: Identify employees responsible for maintaining and updating knowledge to ensure relevance and accuracy.
- Specialist training: Regular participation in training courses, conferences and trade fairs as well as the use of specialist publications to bring external knowledge into the company and disseminate it.
- QM wiki as a knowledge platform: Creation of a quality management wiki that contains internal regulations and tried-and-tested knowledge and ensures that all contributions are traceable and versioned.
Chapter: 7.2 Expertise
Summary
Section 7.2 of ISO 9001:2015 deals with the competence requirements for employees who influence an organisation’s quality management system (QMS). Companies are required to ensure that all employees have the necessary competences for their tasks.
What does that mean in concrete terms?
This means that companies must identify, assess and promote the necessary skills, knowledge and experience of their employees in order to ensure the quality of their products and services. This includes the definition of requirements, the assessment of existing competences and the implementation of training measures.
How can this be implemented in practice?
- Identification of competence requirements: Defining the skills and knowledge required for each role in the organization, especially those that have a direct impact on quality.
- Assessment of existing competences: Checking whether employees already have the competences required for their roles and identifying gaps that need to be closed through further training measures.
- Planning and organizing training courses: Organizing training and further education measures to ensure that all employees acquire and maintain the knowledge and skills required for their tasks.
- Documentation and review of effectiveness: keeping records of training provided and evaluating its effectiveness to ensure that the training has led to an improvement in competencies.
- Ongoing skills development: Regular review and adjustment of skills requirements and training programs to keep pace with technological changes, new market requirements and internal process changes.
By implementing these steps, organizations can not only improve the skills of their employees but also improve the overall performance of their QMS and increase customer satisfaction.
Chapter: 7.2 Expertise
Summary
Section 7.2 of ISO 9001:2015 aims to ensure that all employees whose activities influence quality are sufficiently qualified and continuously trained.
What does that mean in concrete terms?
This means that not every employee in the company has to be highly qualified, but those whose work has a direct or indirect influence on quality – from production to IT – must have the necessary qualifications. Each quality-relevant function should have a clear qualification profile that defines the required training, certificates and experience.
How can this be implemented in practice?
- Qualification profiles and matrix: Introduction of qualification profiles for each position that has quality-relevant tasks and a matrix that shows the skills of employees in different areas. This helps to maintain an overview and plan targeted training courses.
- Identifying training needs: Regular assessments of employees’ actual skills against the requirements of their roles to determine where training is needed.
- Carrying out and evaluating training courses: Organisation and implementation of training measures tailored to the identified needs. The success of these training courses should not be evaluated immediately after the measure, but after a phase of practical application.
- Transparency tools: Use of tools such as company wikis and qualification matrices to document and manage employee competences in order to simplify the process for each certification and make it transparent.
- Ensuring comprehension during training courses: Adapting training content to the language skills of employees to ensure that critical information is correctly understood, as illustrated in the example of the cleaning service provider with multilingual tests.
- Documentation and verification: Keep records of training and qualifications in the form of certificates, certificates of attendance and minutes in order to be able to prove, if necessary, that employees have successfully completed the required training.
These measures can ensure that all employees who perform quality-related functions have the necessary expertise and that these competencies are regularly updated and expanded to meet the requirements of the company and the ISO standard.
Chapter: 7.3 Consciousness
Summary
Section 7.3 of ISO 9001:2015 requires that employees are aware of the relevance and importance of their activities within the quality management system. This includes an understanding of how they can contribute to achieving the quality objectives.
What does that mean in concrete terms?
This means that every team member must understand how his or her work influences the quality of the products or services. Employees should know the company’s quality policy, understand the specific contributions they make and recognize the possible consequences of non-compliant results.
How can this be implemented in practice?
- Communication of the quality policy: Ensure that the quality policy is known and understood by all employees. This can be done through regular meetings, notices in the workplace or via internal communication platforms.
- Quality awareness training: Organise regular training courses and workshops to raise awareness of quality issues. These should be tailored to the various roles in the company and contain practical examples of how employees can contribute to quality.
- Feedback and participation: Encourage employees to give feedback and participate in discussions about quality policy and objectives. This promotes a deeper understanding and commitment.
- Recognize contributions to quality: Implement a system to recognize and reward employees who actively contribute to improving quality. This can increase motivation and awareness of the importance of their work.
- Check understanding: Conduct regular reviews to ensure that all employees understand the quality policy and their role within the quality management system. This could be done through informal discussions or more formal tests.
Chapter: 7.4 Communication
Summary
Section 7.4 of ISO 9001:2015 emphasizes the importance of effective communication as the basis for a functioning quality management system (QMS). It encourages organizations to establish, implement and maintain internal and external communication processes.
What does that mean in concrete terms?
In concrete terms, this means that companies must clearly define what is communicated, when, how and with whom in order to ensure the effectiveness of their QMS. This includes the communication of quality objectives, policies and procedures to all parties involved.
How can this be implemented in practice?
- Develop a communication strategy: Create a comprehensive strategy that defines how information is communicated within the organization and externally. This should include the selection of communication channels, frequency and content.
- Regular updates and meetings: Hold regular meetings and updates to ensure that all employees are informed about the latest quality objectives and standards.
- Establish feedback systems: Implement systems to collect feedback from employees, customers and other stakeholders. This helps to continuously improve communication processes.
- Employee training: Ensure that all employees are trained in effective communication, especially those who interact directly with customers and suppliers.
- Utilise technology: Utilize modern technologies such as intranet platforms, email systems and social media to make communication efficient and far-reaching.
- Documentation and review: Document all communication processes and regularly review their effectiveness. Adapt strategies where necessary to further improve communication.
Through these measures, organizations can ensure that their communication processes help to effectively support the objectives of the quality management system and make the organization as a whole stronger.
Chapter: 7.5 Documented information
Summary
Section 7.5 of ISO 9001:2015 regulates requirements for the documented information of a quality management system (QMS). It requires organizations to manage the creation, updating and control of this information to ensure compliance and support the effectiveness of the QMS.
What does that mean in concrete terms?
This means that companies must ensure that all necessary documents are created, maintained, made accessible and updated as required. This includes documents that are necessary for the planning, implementation and monitoring of processes, as well as records that serve as proof of conformity with the specified requirements.
How can this be implemented in practice?
- Document creation and updating: Develop procedures for creating and updating documented information to ensure that documents are clear, accurate and up to date. This also includes the approval of documents by authorized persons.
- Control documented information: Implement a document management system that regulates the access, distribution, storage and secure disposal of old documents.
- Accessibility and findability: Ensure that documented information is easily accessible and findable for those who need it. This can be facilitated by the use of digital systems such as an intranet or specialized software solutions for document management.
- Protection of sensitive information: Take measures to protect the integrity and confidentiality of sensitive documented information. This includes security precautions against unauthorized access and data loss.
- Monitoring and review: Conduct regular reviews to assess the adequacy and effectiveness of the documented information. This helps to identify potential problems and initiate improvement measures.
- Compliance with legal requirements: Ensure that all documented information complies with the relevant legal and regulatory requirements.
By implementing these steps, an organization can establish a robust system for managing its documented information that will help improve QMS performance and meet compliance requirements.