This article aims to elucidate the key aspects of ISO 9000 and ISO 9001, shedding light on the iso 9001 vs 9000 debate, pinpointing the iso 9000 iso 9001 difference, and guiding organizations in choosing the standard that best fits their specific requirements. It will provide a comprehensive overview of each standard, delve into their key differences, and explore the shared benefits, thereby enabling a well-informed decision-making process. Furthermore, a step-by-step guide to ISO 9001 certification, along with operational benefits and tips for successful certification, will be discussed, offering a roadmap for businesses aiming to achieve and maintain this coveted certification.
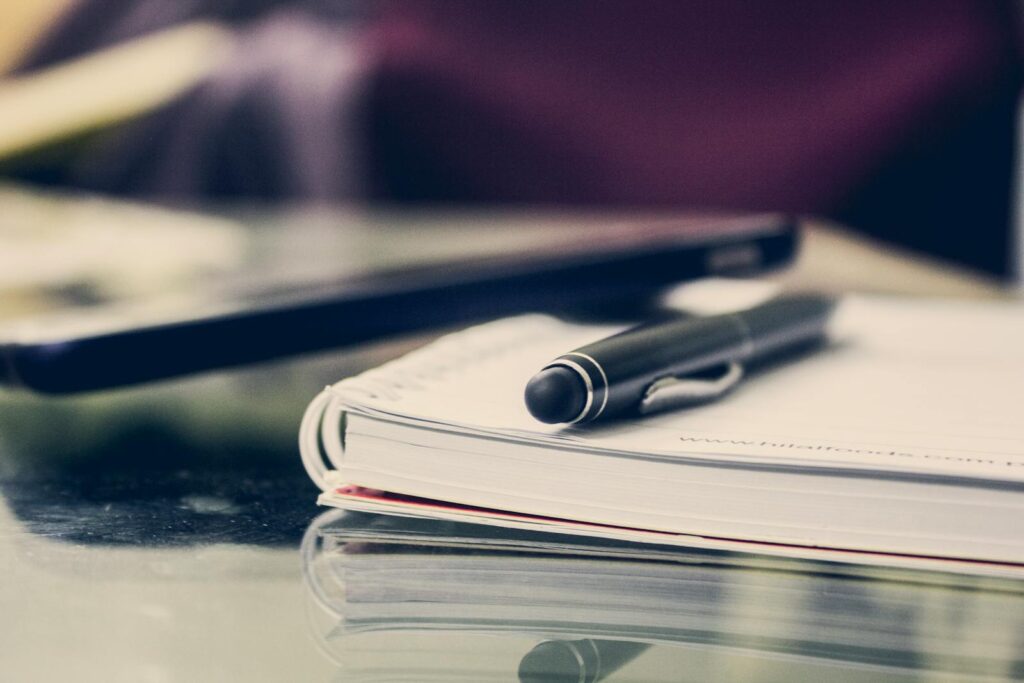
Overview of ISO 9000
ISO 9000 is a series of standards designed to assist organizations in establishing, documenting, and maintaining an effective quality management system (QMS). Defined by the International Organization for Standardization (ISO), these standards are not confined to any single industry and can be implemented by organizations of any size. They aim to enhance customer satisfaction through the effective application of a QMS, including processes for continual improvement and assurance of conformity to customer and applicable statutory and regulatory requirements.
First published in 1987, ISO 9000 has undergone several revisions to address the evolving needs of organizations globally. The most recent updates, ISO 9000:2015 and ISO 9001:2015, were released in September 2015. These revisions were made with the objective of simplifying the standards and making them more accessible to all organizations, regardless of size or sector.
The ISO 9000 family includes:
- ISO 9001:2015: Quality Management Systems – Requirements
- ISO 9000:2015: Quality Management Systems – Fundamentals and Vocabulary
- ISO 9004:2018: Quality Management – Quality of an Organization – Guidance to Achieve Sustained Success
- ISO 19011:2018: Guidelines for Auditing Management Systems
These standards are built on seven key principles of quality management which are intended to be a guide for senior management to lead organizational improvement:
- Customer focus
- Leadership
- Engagement of people
- Process approach
- Improvement
- Evidence-based decision making
- Relationship management
ISO 9000 serves as the foundational guideline that lays out the fundamentals and vocabulary for quality management systems, making it the starting point for organizations seeking to implement a QMS. It is particularly noted for its role in helping organizations document the necessary elements of a quality system effectively. This documentation is crucial for maintaining an efficient system that can adapt to the changing needs of the customer, meet regulatory requirements, and aim for continual improvement.
The adoption of ISO 9000 standards is voluntary, yet they carry significant weight in global commerce. Organizations that achieve certification to ISO 9001, for example, demonstrate to stakeholders that they adhere to internationally recognized standards of quality. While obtaining certification can be resource-intensive, the benefits of implementing these standards include improved operational efficiency, enhanced customer satisfaction, and increased competitiveness in the market.
ISO 9000 remains one of the most widely recognized and implemented quality management system standards worldwide, providing a trusted framework for organizations to ensure their products and services consistently meet customer and regulatory requirements.
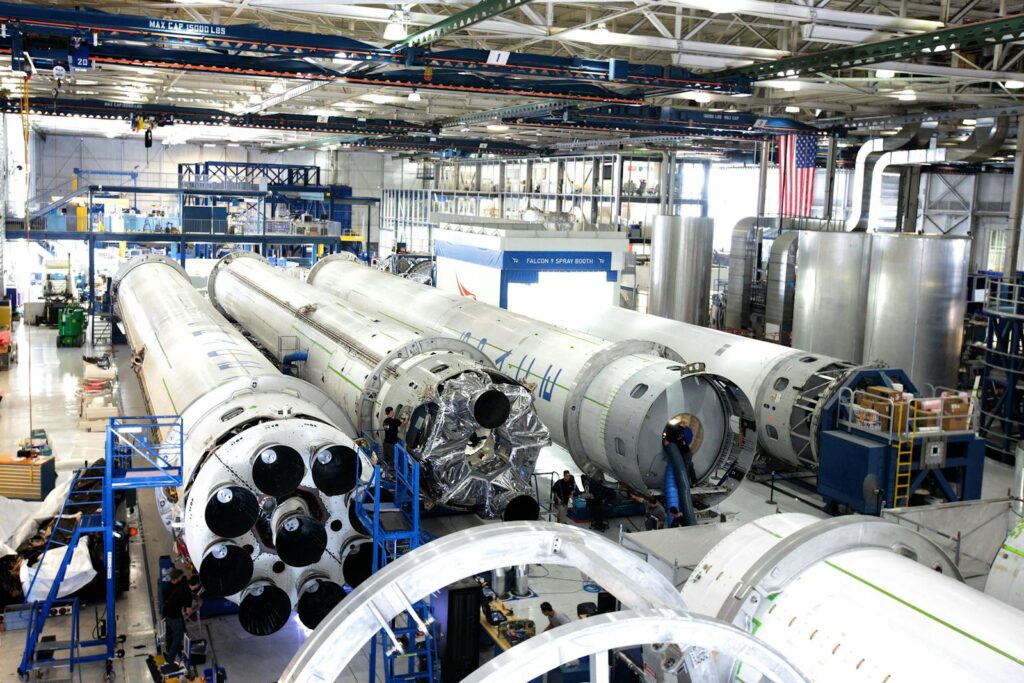
Overview of ISO 9001
ISO 9001 is an internationally recognized standard for quality management systems, specifically designed to help organizations ensure that they meet both customer and regulatory requirements while enhancing customer satisfaction through effective system processes. This standard is part of the broader ISO 9000 family but stands out as the only standard within the series that organizations can certify to.
Key Elements and Requirements of ISO 9001:2015
ISO 9001:2015 sets out the criteria for a quality management system and is structured to be implemented by any organization, regardless of its type or size, or the products and services it provides. The standard is based on a number of quality management principles including a strong customer focus, the motivation and implication of top management, the process approach, and continual improvement.
- System and Process Approach: ISO 9001:2015 employs a process approach which incorporates the Plan-Do-Check-Act (PDCA) cycle and risk-based thinking. This approach enables organizations to plan their processes and their interactions efficiently.
- Leadership and Commitment: The standard emphasizes the importance of leadership and commitment from top management. Leaders are required to demonstrate their commitment to the QMS by ensuring customer focus, defining and communicating the quality policy, and ensuring that the QMS achieves its intended results.
- Customer Focus: Organizations are required to consistently provide products and services that meet customer and applicable statutory and regulatory requirements. It aims to enhance customer satisfaction through the effective application of the system.
- Performance Evaluation: It involves monitoring and measuring processes and products against policies, objectives, and requirements and reporting the results. ISO 9001:2015 requires organizations to perform regular internal audits and management reviews to ensure the effectiveness of the QMS.
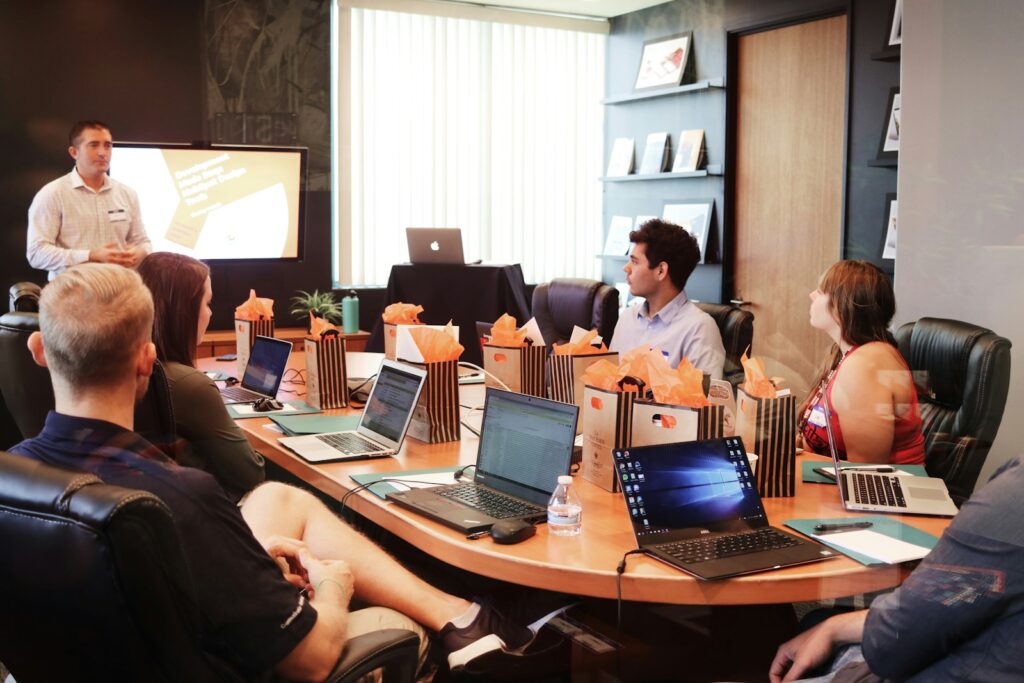
Operational Benefits and Implementation
Implementing ISO 9001:2015 can help organizations improve their internal management by focusing on the major areas of process efficiency, customer satisfaction, and product improvement. Organizations that adopt this framework commit to quality, gain a competitive edge, and can access new markets. Benefits include improved operational performance, a solid foundation for sustainable development initiatives, and increased customer trust and satisfaction.
Organizations that implement ISO 9001:2015 have reported significant improvements in their operations, including better regulatory compliance, reduced waste, and improved productivity. The standard provides the necessary tools to ensure that quality management becomes an integral part of their business operations, fostering a culture of continuous improvement.
ISO 9001:2015 encourages organizations to use a quality management system as a strategic tool, enhancing their ability to consistently provide products and services that meet customer requirements and increasing their competitiveness in the market. It also helps in identifying risks and opportunities associated with the context and objectives of the organization, thereby ensuring sustained business success through adaptable and agile processes.
Key Differences Between ISO 9000 and ISO 9001
Scope and Focus
The primary distinction between ISO 9000 and ISO 9001 lies in their scope and focus within the realm of quality management standards. ISO 9000 serves as a foundational guideline, offering a comprehensive framework and vocabulary that underpins all other standards in the series, including ISO 9001. It is designed to help organizations understand and implement the principles of quality management effectively. In contrast, ISO 9001 is more specific, focusing on the requirements that organizations must meet to establish a robust Quality Management System (QMS). This standard is action-oriented and is used by organizations to demonstrate their ability to consistently provide products and services that meet customer and regulatory requirements.
Certification Possibility
ISO 9001 stands out within the ISO 9000 family as the only standard that offers certification. Achieving ISO 9001:2015 certification is a mark of assurance that an organization adheres to the guidelines of the standard and fulfills its specific requirements. This certification process involves a detailed review of the organization’s processes and a commitment to maintaining extensive documentation to prove compliance.
On the other hand, ISO 9000 does not offer certification but provides essential groundwork that supports organizations in preparing for ISO 9001 certification.
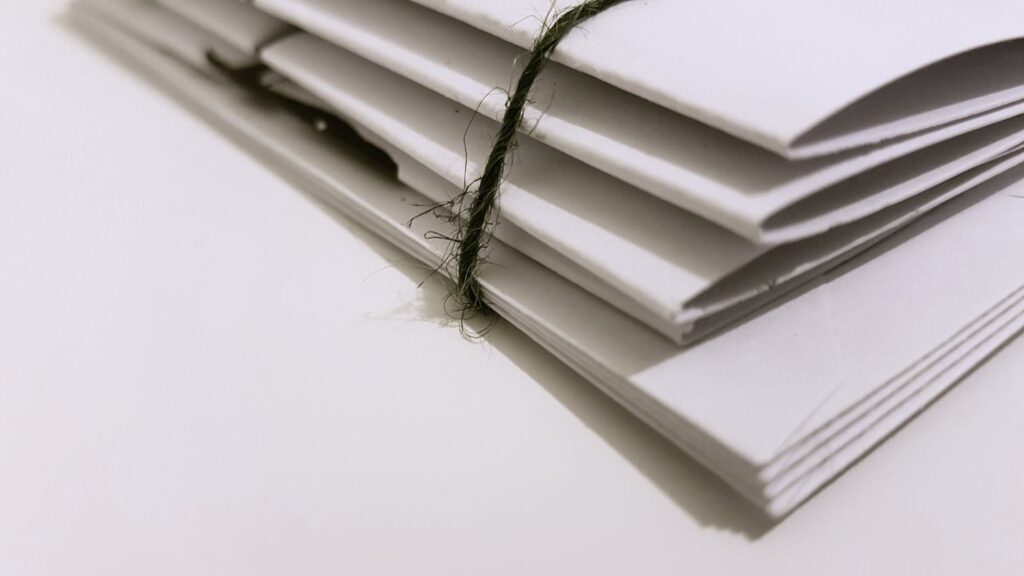
Implementation Requirements
Implementing ISO 9001 is a more rigorous process compared to the general guidance provided by ISO 9000. ISO 9001 implementation requires a gap analysis, internal audits, and a systematic approach to managing and improving quality processes that are directly tied to customer satisfaction. Organizations must establish a detailed quality policy, set measurable objectives, and engage in continuous improvement to meet the stringent requirements of ISO 9001. Conversely, ISO 9000 primarily equips organizations with the necessary knowledge and terminology to understand and support a quality management system without the requirement for specific procedural implementations.
Shared Benefits of ISO 9000 and ISO 9001
ISO 9000 and ISO 9001, while distinct in their requirements and implementation, share several core benefits that enhance organizational performance across various sectors. These standards are designed not only to bolster quality management systems but also to foster a culture of continuous improvement and customer satisfaction. Here, we explore the shared advantages that these standards offer to organizations that adopt them.
Enhanced Customer Satisfaction
Both ISO 9000 and ISO 9001 place a strong emphasis on customer satisfaction. This focus is pivotal as it drives organizations to consistently deliver products and services that meet customer expectations and regulatory requirements. By implementing these standards, companies can better understand customer needs and reduce the likelihood of errors, leading to improved customer loyalty and a stronger reputation in the market.
Improved Operational Efficiency
The guidelines provided by ISO 9000 combined with the specific requirements of ISO 9001 help organizations streamline their operations. This integration leads to more efficient use of resources, reduced waste, and cost savings. Moreover, the process approach advocated by both standards encourages organizations to identify interdependencies among processes, leading to enhanced decision-making and improved operational performance.
Continual Improvement
Continual improvement is a cornerstone of both ISO 9000 and ISO 9001. These standards encourage organizations to constantly seek ways to improve their processes and quality management systems. This ongoing pursuit of excellence not only helps in adapting to the changing market conditions but also drives innovation within the organization.
Increased Marketability
Certification to ISO 9001, supported by the foundational guidelines of ISO 9000, significantly enhances a company’s credibility and marketability. This recognition opens up new market opportunities and can be a deciding factor in contract awards, particularly when competing against companies without certification. It serves as a testament to the organization’s commitment to quality, attracting new customers and retaining existing ones.
Regulatory Compliance
Both standards provide a framework that helps organizations comply with applicable statutory and regulatory requirements. By aligning organizational processes with the stipulations of ISO 9000 and ISO 9001, companies can more effectively manage their compliance obligations, reducing the risk of penalties and legal issues.
Flexibility for All Organization Sizes
ISO 9000 and ISO 9001 are designed to be adaptable, making them suitable for businesses of all sizes, from small startups to large multinational corporations. This flexibility ensures that organizations can tailor the principles and requirements of the standards to fit their specific operational needs and objectives.
By adopting ISO 9000 and ISO 9001, organizations not only commit to quality and efficiency but also position themselves to achieve sustainable success through improved customer relations, operational excellence, and continuous improvement. These shared benefits underscore the importance of integrating quality management systems into the core operational strategy of any forward-thinking organization.
Step-by-Step Guide to ISO 9001 Certification
Gap Analysis
The initial step toward ISO 9001 certification involves conducting a comprehensive gap analysis. This process assesses the current state of your organization’s quality management system (QMS) against the requirements of ISO 9001. It identifies areas where your practices may not fully comply with the standards, allowing you to pinpoint critical areas for improvement. Utilizing a gap analysis checklist, organizations can systematically review and document each aspect of their existing system, highlighting discrepancies and formulating an action plan to address these gaps. This structured approach ensures that all necessary adjustments are identified early, facilitating a smoother transition to compliance.
Internal Audits
Following the gap analysis, internal audits are essential to ensure that the newly implemented processes conform to ISO 9001 standards. These audits serve as critical self-checks, allowing organizations to assess the effectiveness and compliance of their QMS internally before facing external certification audits. Conducting these audits involves evaluating processes, interviewing staff, and reviewing compliance with both ISO 9001 requirements and internal procedures.
Organizations may choose to perform these audits in-house or hire external auditors to bring an unbiased perspective. Regular internal audits not only prepare the organization for certification but also foster a culture of continuous improvement.
Preparation for Certification
The final preparatory step for ISO 9001 certification is ensuring that all organizational processes and documentation align with the standard’s requirements. This includes organizing work areas, updating or discarding outdated documents, and training staff to be audit-ready. Preparing for the certification audit is crucial as it involves a thorough review by an external auditor who will assess the entirety of your QMS. Organizations should aim to resolve any nonconformities identified during internal audits prior to this stage. Proper preparation ensures that your organization presents itself effectively, demonstrating full compliance and operational excellence during the certification audit.
Operational Benefits of ISO 9001 Certification
Achieving ISO 9001 certification offers a multitude of operational benefits that can significantly enhance the performance and credibility of any organization. This section explores how the certification aids in refining quality management systems, thereby ensuring sustained business improvement and customer satisfaction.
Streamlined Processes and Increased Efficiency
ISO 9001 certification requires organizations to establish a clear, systematic approach to managing their processes. This includes the development of a robust quality management system (QMS) that emphasizes efficiency and consistency. By identifying inefficiencies and implementing necessary improvements, companies can reduce errors and minimize waste, leading to significant cost savings. Additionally, well-documented standard operating procedures under ISO 9001 ensure that all processes are clear and consistent, which enhances overall efficiency and productivity.
Enhanced Customer Satisfaction
A core focus of ISO 9001 is meeting customer requirements and boosting their satisfaction. Organizations are compelled to continuously improve their QMS, which leads to consistently high-quality products and services. This dedication to quality can result in higher customer loyalty, positive referrals, and repeat business, ultimately contributing to a stronger market position.
Improved Product Quality
The certification mandates a documented system for production and quality testing, which significantly elevates the quality of the products or services offered. This not only meets the customer’s expectations consistently but also strengthens the organization’s reputation in the market.
Business Growth and Market Opportunities
ISO 9001 certification opens up new market opportunities, particularly in sectors where certification is a prerequisite. It enables organizations to participate in tenders for both small and large projects, significantly enhancing their business growth prospects. The certification is often a requirement for suppliers in many industries, which positions certified companies as credible and reliable partners.
Enhanced Employee Satisfaction and Job Security
The clarity in processes and the structured environment fostered by ISO 9001 contribute to greater employee job satisfaction. Employees are more secure and engaged when they understand their roles and responsibilities clearly, which is facilitated by the standardized procedures outlined in the certification.
Compliance and Risk Management
ISO 9001 helps organizations comply with statutory and regulatory requirements, reducing the risk of non-compliance penalties. Moreover, the certification prepares businesses to effectively manage unexpected issues, such as product failures or customer complaints, with established procedures for resolving such problems efficiently.
Cost Management and Profitability
Organizations that implement ISO 9001 can achieve more efficient control over their processes, which leads to reduced operational costs. Regular audits and reviews as part of the certification process ensure that processes do not become outdated or inefficient, thereby maintaining cost-effectiveness and boosting profitability.
By integrating these operational benefits, organizations not only adhere to internationally recognized standards but also enhance their competitive edge and operational sustainability. The ISO 9001 certification thus serves as a valuable tool for businesses aiming to optimize their quality management practices and achieve long-term success.
Tips for Successful Certification
Selecting the right ISO 9001 implementation strategy is crucial for your quality management system’s success. Here are practical tips to navigate this process effectively:
- Comprehensive Gap Analysis: Conduct thorough and, if necessary, multiple mini gap analyses during the documentation and implementation stages. This is especially effective for small and medium-sized businesses undertaking ISO 9001 implementation in-house. These analyses help pinpoint critical areas that need attention, ensuring that all ISO 9001 requirements are adequately addressed.
- Utilization of Documentation Templates: Prepare all ISO documents meticulously. Using documentation templates can simplify this process. These pre-written documents, designed to be tailored to your company’s needs, come with customization instructions. Ensure that the templates you choose have comprehensive customization instructions that align with your specific needs.
- Engage and Prepare Your Staff: Empower your staff by involving them in the redesign of work processes to align with ISO 9001 requirements. Reduce audit anxiety by clearly explaining what to expect from the audit and the auditor. Train staff on how to interact with auditors and answer questions truthfully without volunteering additional information. Rehearse typical auditor questions to ensure your team understands their roles and the importance of their daily activities in aligning with the company’s quality policy.
- Resource Allocation: Allocate adequate resources, including trained personnel and dedicated time, to maintain your quality management system. This ensures that the system continuously meets the requirements of ISO 9001.
- Performance Indicators and Internal Audits: Establish key performance indicators to measure the success of your quality management system. Regularly track these indicators and conduct periodic internal audits. These audits help evaluate the effectiveness of your quality management system and correct potential nonconformities.
- Continuous Learning and Improvement: Stay current with changes to ISO 9001 and learn from the best practices of other organizations. This can provide valuable insights and opportunities for improvement in your own system.
By following these steps and preparing thoroughly for the certification process, organizations can enhance their chances of achieving ISO 9001 certification, thereby improving their operational efficiency and market credibility.
Conclusion
Navigating the intricate world of ISO standards, particularly the differentiation between ISO 9000 and ISO 9001, is pivotal for organizations aiming for operational excellence and customer satisfaction. The article provided an authoritative exploration of both standards, delving into their objectives, key differences, and the operational benefits that accompany adherence to these benchmarks. We emphasized the strategic importance of choosing the right standard to not only meet but exceed quality management expectations, thereby underscoring our mission to guide professionals through the complexities of quality management systems with clarity and expertise.
Understanding the nuanced differences and shared benefits of ISO 9000 and ISO 9011 lays the foundation for effective quality management within organizations of any size or scope. These standards, when correctly implemented, propel businesses towards sustainable success through improved efficiency, customer satisfaction, and market competitiveness. For those professionals seeking to elevate their organizational standards and achieve ISO certification, our guidance does not end here.
Are you ready to improve your quality management? Contact us now and let’s discuss how we can work together to achieve your ISO certification goals. Our commitment remains to provide you with comprehensive, structured, and easily digestible insights, empowering your journey towards operational excellence and quality leadership.
FAQs
Which ISO standard is recommended for businesses new to ISO standards?
ISO 9001 is the recommended standard for businesses that are new to ISO standards. It outlines the necessary requirements for establishing a quality management system (QMS) within a business.
What distinguishes ISO 9001 from AS9100 in terms of industry application?
The primary distinction is that AS9100 is tailored specifically for the aerospace industry, whereas ISO 9001 is applicable to businesses across all industries.
Who is the target audience for ISO 9000 guidelines?
ISO 9000 guidelines are versatile and can be applied to any organization, regardless of its industry or size. They are designed to help companies satisfy customer requirements, meet regulatory standards, and foster continual improvement.
Is ISO 9000 still a relevant standard today?
Yes, ISO 9000 remains highly relevant and is part of a critical series of 14 quality management standards. The most recent version, ISO 9001:2015, provides detailed guidance on setting up an effective quality management system to ensure the delivery of high-quality products and services.