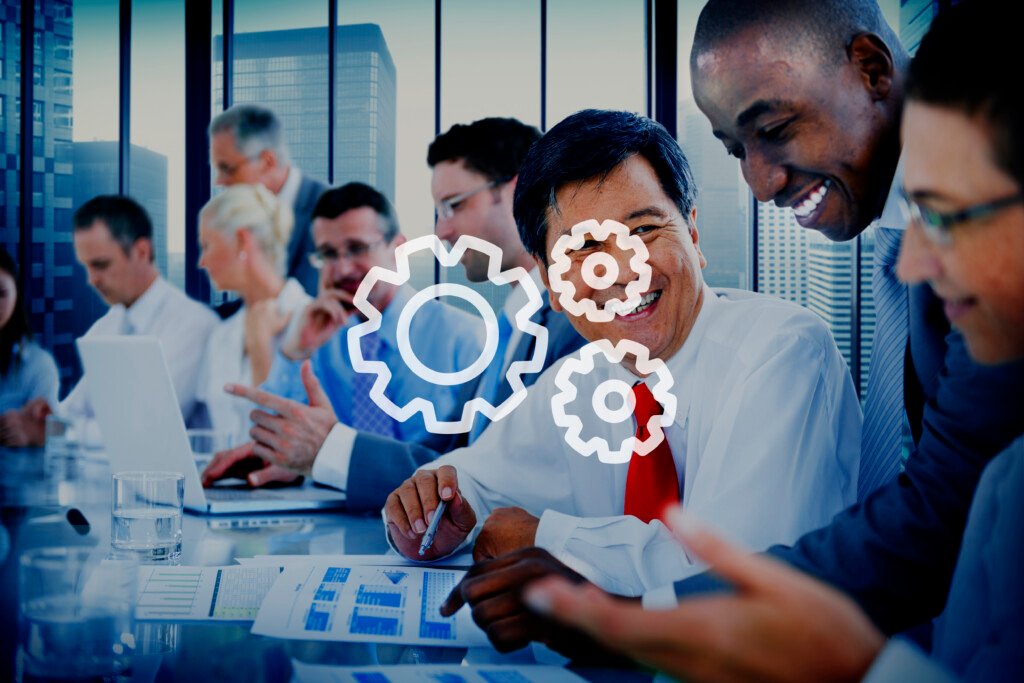
Understanding Clause 8 “OPERATION” of ISO 9001:2015
ISO 9001:2015 SECTION 8 “OPERATION”
Companies are aware of the importance of excellent operational performance and meeting customer expectations. The objectives of clause 8 of ISO 9001:2015 focus on various aspects of operations, including operational planning and control, customer communication, design and development, control of outsourced processes, and production and service delivery. These objectives form the basis for the effective implementation of operational processes and the consistent delivery of products and services. The guiding clause 8 deals with both internal and outsourced processes to meet the needs of the organization.
Centerpieces
- Operational planning and control to meet product and service requirements, including setting criteria for processes, determining resource requirements and controlling planned changes.
- Effective communication with customers and understanding their needs are crucial for customer satisfaction and loyalty.
- The definition of product and service requirements includes the determination of acceptance criteria, required resources and the control of planned changes to mitigate adverse effects.
- Design and development processes must align with product requirements, establish key performance metrics and provide documented information to ensure reliability of process execution.
- Risk assessment and implementation processes play a crucial role in ensuring successful design and development outcomes.
8.1 Operational planning and control
Clause 8.1 of ISO 9001:2015 requires organizations to plan, implement and control processes to meet the product and service requirements described in clause 4.4 (Quality management system and its processes) and clause 6.1 (Risk management measures and options) and to implement the specified measures. This includes:
- Determination of product and service requirements.
- Definition of criteria for process and product acceptance.
- Identify the resources required for compliance.
- Implementation of process controls according to specific criteria.
- Maintain documented information to ensure that planned processes are carried out and to demonstrate compliance.
- Control of planned changes and mitigation of unintended consequences.
- Ensuring the control of outsourced processes in accordance with section 8.4 (Control of externally provided products and services).
The focus is on the effective management of processes that are carried out internally or externally to meet customer requirements. Operational processes include various activities such as sales, design, production, shipping, etc. The processes must document these procedures to the extent that the organization considers important. This means that the decision as to whether a process is documented or not is at the discretion of the organization. The risk-based approach applies again. The documentation does not necessarily have to be summarized in one document. Instead, it can be spread over several documents such as drawings, setup instructions, etc., as long as they are easily accessible. Companies may consider using product or project quality plans to detail processes, resources, acceptance criteria and monitoring controls. The focus should be on avoiding errors and achieving quality targets, e.g. reducing the error rate or improving delivery reliability.
External processes must also meet the requirements of ISO 9001, and performance indicators should measure process and product performance, focusing on reducing variation and waste while improving productivity and quality.
8.2 Requirements for products and services
To ensure the conformity of products and services, ISO 9001: 2015 Chapter 8 emphasizes the need for companies to define clear and specific requirements for their products and services. This is of crucial importance for the management system, as it forms the basis for successful production and service provision.
Here are the most important points you should bear in mind:
- Determining the requirements for products and services :
- Companies must clearly define the requirements for their products and services, taking into account the needs and expectations of their customers.
- These requirements should be specific, measurable, realistic, relevant and time-bound (SMART) and enable effective planning and implementation.
- Ensuring compliance with the regulations :
- By defining clear requirements, companies can ensure that their products and services meet the desired quality standards.
- This includes defining acceptance criteria, carrying out inspections and tests and implementing quality control measures throughout the entire production and service process.
8.2.1 Customer requirements and communication
Effective communication of customer requirements is essential to ensure the delivery of high quality products and services. Chapter 8, “Operations”, emphasizes the importance of understanding and meeting customer needs. It’s not just about identifying customer requirements, but also about communicating and documenting them effectively throughout the company.
To achieve this, companies should establish clear communication channels with customers and ensure that their requirements are understood and translated into actionable steps. This can be achieved through various means, e.g. meetings, surveys and feedback mechanisms. By actively interacting with customers and gathering their input, companies can gain valuable insights and improve their understanding of customer expectations.
The following table shows the most important aspects of customer requirements and communication:
Aspect | Description |
Determine the need | Companies should identify and document their customers’ requirements, including explicit and implicit expectations. |
Communication | Clear and effective communication channels should be established to ensure that customer requirements are understood by all parties. |
Requirements for the document | Customer requirements are documented in a systematic and organized manner to ensure that they are easily accessible and retrievable. |
Implement requirements | Companies must take the necessary measures to meet customer requirements and align their operational processes accordingly. |
Monitoring satisfaction | Customer satisfaction must be monitored regularly to identify gaps between customer expectations and the products/services delivered. |
8.2.2 Determining the requirements for products and services
Identifying product and service requirements is a crucial aspect when it comes to ensuring customer satisfaction and delivering high-quality offerings. To achieve this, organizations must create controlled conditions and define criteria for the acceptance of products and services. This involves the following:
- Determination of product and service requirements :
- Companies must clearly define the specific requirements for their products and services. This also includes determining customer needs and expectations as well as the legal requirements that must be met.
- Definition of criteria for the processes and acceptance of products and services :
- Companies must define the criteria on the basis of which they assess the conformity of their products and services. This also includes the definition of quality standards and specifications that must be adhered to.
In addition to these internal requirements, organizations must also consider externally provided processes. This involves the management and control of processes that are outsourced to external parties. It must be ensured that these processes have the same level of quality and conformity as internal processes.
The review is a crucial step in determining the requirements for products and services. Companies must have procedures in place to check whether their products and services meet the defined criteria and satisfy customer requirements. This may include carrying out inspections, tests or other forms of assessment to ensure product quality.
8.2.3 Review of product and service requirements
Reviewing product and service requirements is an essential step in ensuring customer satisfaction and the provision of high-quality offerings. It is a crucial aspect of quality management, as it is about understanding and meeting customer expectations. By checking these requirements, companies can ensure that their products or services meet the needs and preferences of their customers.
During the review process, companies must consider various factors, such as the specific features and functions of the product or service, any regulatory or legal requirements and the overall customer experience. This review helps companies identify areas where improvements can be made to increase customer satisfaction and provide a better product or service.
In addition, the capabilities and limitations of the suppliers must also be taken into account when reviewing the requirements. Companies must assess whether their suppliers meet the specified requirements and can maintain the desired level of quality. This ensures that the necessary procedures are in place to control the production or supply of the product or service.
8.2.4 Changes to the requirements for products and services
Changes to product and service requirements involve adapting and updating the necessary criteria to meet changing customer needs and preferences. This process requires careful thought and planning to ensure that the company can effectively design and develop products and services that meet customer expectations. This also includes the proper provision of services, including the release of products and services to customers.
In order to successfully manage these changes, the company should introduce control plans that describe the necessary steps and measures. These control plans should cover various aspects, such as: e.g:
- Design and development: This involves the creation and improvement of products and services based on customer requirements. The organization should take a systematic approach to design and development and ensure that the necessary resources and criteria are in place.
- Provision of services: This refers to the provision and execution of services for customers. The organization should have clear processes and criteria for the provision of services to ensure that they are delivered efficiently and effectively.
- Release of products and services : This refers to the final stage of delivering products and services to customers. The company should take steps to ensure that products and services meet the required standards before they are delivered to customers.
In addition to these internal processes, the organization can also commission external providers to meet certain requirements. In such cases, the organization should have control measures in place to ensure that these external providers comply with the required criteria and standards.
8.3 Design and development of products and services
In order to effectively adapt and update the required criteria to changing customer needs and preferences, the company must introduce robust procedures for the design and development of products and services.
8.3.1 General
Section 8.1 of ISO 9001:2015. This chapter focuses on the organization’s responsibility to plan, implement and control the processes necessary to meet the requirements for the delivery of products and services. The ultimate goal of the design and development process is to create products and services that not only meet customer requirements, but are also in line with the company’s quality objectives. This requires a systematic and well-documented approach that incorporates feedback from customers and stakeholders to continuously improve and refine the design and development process.
8.3.2 Design and development planning
Design and development planning is a critical aspect of ensuring the effective implementation and control of processes in accordance with the requirements of ISO 9001:2015 clause 8. This planning process includes the determination of product and service requirements, the definition of criteria for the processes and the acceptance of products and services as well as the determination of the resources required to fulfill the defined requirements. The aim of design and development planning is to ensure that operational activities are carried out in a controlled manner to meet customer approval and specified requirements.
- Definition of criteria for the processes and for the acceptance of products and services
- Determining the resources required to fulfill product and service requirements
- Implementation of process control according to the defined criteria
- Maintenance and storage of documented information to prove the conformity of products and services with the requirements
- Monitoring planned changes and reviewing the consequences of unintended changes, taking the necessary measures to mitigate negative effects
- Ensuring that the outsourced processes are controlled in accordance with the requirements
8.3.3 Design and development contributions
Design and development contributions are about gathering the necessary information and requirements for the creation of products and services that meet customer needs and fulfill certain standards and criteria.
To provide a clear understanding of the design and development contributions, two sub-lists illustrating the key elements are provided here:
- Information procurement
- Conducting market research to determine customer needs, preferences and expectations.
- Gather relevant technical information, e.g. industry standards, regulations and best practices.
- Identification of requirements :
- Determine the functional and performance requirements for the product or service.
- Define specific criteria or specifications that must be met, such as: B. Quality standards or safety regulations.
It is important to note that these inputs must be documented and communicated to all those involved in the design and development process. This ensures a common understanding of the project goals and requirements and facilitates effective collaboration and decision-making.
8.3.4 Design and development controls
Design and development controls refer to the comprehensive measures implemented to ensure systematic and controlled execution of the design and development processes. These measures aim to ensure high quality and effectiveness by defining clear criteria for the design and implementation of these processes. This includes careful planning, the selection and deployment of qualified personnel, the provision of suitable equipment and materials and the continuous monitoring and evaluation of all design and development activities. The aim is to ensure consistent quality control and increased efficiency at all stages of the process, from initial planning to final delivery of the products or services.
Companies must keep records and documentation of design and development activities. This documentation serves as proof of compliance and helps to ensure consistency and traceability throughout the design and development process.
8.3.5 Design and development results
ISO 9001:2015 clause 8.3 emphasizes the importance of design and development results for maintaining operational effectiveness. The organization must ensure that
- The results of design and development must match the requirements.
- The development results are suitable for subsequent processes in product and service creation.
- The requirements for monitoring and measurement as well as the applicable acceptance criteria are defined.
- This ensures that the products or services are suitable for the intended purpose and safe use.
- This information, which originates from the design and development process, is documented.
By clearly defining design and development outcomes, companies can ensure consistency, accuracy and compliance with customer requirements. These results serve as a reference point for evaluating the effectiveness of existing design and development processes. Companies should also consider the importance of documenting these results to demonstrate compliance and facilitate traceability. This documentation may include design data sets, test reports and validation results.
8. 3.6 Design and development changes
The organization shall systematically identify, evaluate and manage changes that occur during the design and development phases of products and services to ensure compliance with requirements. The documentation of design and development changes as well as the corresponding verification results, the associated approvals and the measures to avoid negative effects must be maintained.
In addition, a structured process for planning and controlling design and development activities is essential. This process should be established, implemented and consistently maintained. It applies not only to products and services, but also to the associated processes. The most important components of this process include
Planning and control
- Planning of the design phases, including verification, validation, control of the design interface and involvement of the customer.
- Determining the necessary resources for design and development.
- Identify documented information needs to ensure input requirements are met.
Determination of input requirements
- Identification of functional, regulatory, legal and normative requirements.
- Resolution of conflicting requirements.
- Inclusion of lessons learned from previous projects and consideration of the consequences of mistakes.
Design and development controls
- Clear definition of the desired results.
- Carrying out design reviews, verification and validation activities.
- Ensure that the results meet the input requirements and the intended application requirements.
Change management
- Identification, review and control of design and development changes.
- Ensure that the changes do not affect the compliance of products and services.
- Retention of documented information on changes.
The organization carefully follows the steps in section 8.3 for design and development changes and ensures thorough planning, input-output considerations, verification, validation and risk control to meet customer requirements. All change requests, whether internal, customer-oriented or official, are documented and confirmed in writing by the customer. Assessments include comprehensive evaluations of materials, processes, properties, compliance, costs and other factors in accordance with section 6.3 for change planning and section 6.1 for identifying risks and opportunities. Detailed records of changes, reviews, approvals and preventive measures are kept to prevent adverse effects.
8.4 Control of externally provided processes, products and services
Section 8.4 of ISO 9001:2015, which focuses on the control of externally provided processes, products and services.
8. 4.1 General
The organization must ensure that external providers meet the specified requirements. These include situations:
- When external providers deliver products and services that are to be integrated into the company’s own products and services.
- When external providers deliver products and services directly to the customer on behalf of the company.
- If the organization decides to outsource a process or function, it must also ensure that the external provider meets the specified requirements.
To effectively manage these externally provided processes, products and services, the organization must establish criteria for evaluating, selecting, monitoring the performance and re-evaluating external providers. This ensures that the external providers are able to deliver processes, products and services in accordance with the defined requirements. In addition, it is important for the organization to obtain relevant documented information about these activities and any necessary actions resulting from the assessment of the external providers.
8.4.2 Type and scope of control
To ensure effective control of externally provided processes, products and services, the organization must carefully define the nature and scope of the control measures to be applied. This also includes weighing up the potential impact of externally provided processes, products and services on the company’s ability to consistently meet customer and regulatory requirements. The organization must also assess the effectiveness of the controls applied by the external provider.
To determine the nature and scope of the control measures, the organization should:
- Perform monitoring and measurement activities to evaluate the external provider’s performance in delivering compliant products and services.
- Implementation of corrective actions to address non-conformities identified during monitoring and measurement activities.
- Definition of acceptance criteria for externally provided processes, products and services to ensure that they meet the company’s requirements.
- Integrate risk management principles to identify and mitigate potential risks associated with the external provision of processes, products and services.
In addition, the organization must establish and perform verification or other activities to ensure that the externally provided processes, products and services meet the requirements. This may include conducting audits or inspections to verify compliance with the external provider’s processes.
8.4.3 Information for external providers
To ensure the adequacy of the specified requirements prior to submission to external providers, the organization shall communicate to external providers the applicable requirements for products and services to be provided or processed on behalf of the organization. This communication should cover several key areas:
- Specifications for products, services and processes:
External suppliers must understand the requirements for the products and services they will deliver and the processes they will carry out on behalf of the company.
2. approval and release procedure:
External suppliers should be informed of the procedures for approving or releasing products, services, methods, processes or equipment to ensure that they comply with company standards.
3. competence and qualification of staff:
Clarity about the competence and required qualifications of personnel involved in the provision of services or the execution of processes is essential for maintaining quality standards.
4.Interaction with the organization’s quality management system:
External service providers should be informed of their interaction with the organization’s quality management system, including any protocols or procedures they are required to follow.
5. performance control and monitoring:
The organization must communicate the methods used to control and monitor the performance of external service providers and ensure accountability and quality assurance.
6.review activities:
External providers must be informed of any verification activities that the company or its clients intend to carry out on their premises in order to facilitate cooperation and compliance.
In addition, the Company should consider applying a risk-based approach to determine the appropriate level of controls for various external vendors and externally provided processes, products and services. In this way, the company can deploy its resources efficiently and focus on the areas that pose the greatest risks to the quality and delivery of services.
Ultimately, effective communication and control of external suppliers helps the company to meet customer requirements, maintain the integrity of its quality management system and ensure the delivery of high quality products and services. It also enables the company to carry out audits and maintain traceability, which are essential for continuous improvement and customer satisfaction.
8.5 Production and service provision
The provision of production and services includes the execution and delivery of products and services in accordance with the defined criteria and requirements of the organization. To meet the requirements of this section, the organization must have a thorough understanding of the requirements and criteria for the production and service processes.
8.5.1 Control of production and service provision
Effective control of production and the provision of services is essential to ensure compliance with the requirements of ISO 9001:2015 and to maintain the quality of products and services. This includes implementing processes and controls to ensure that products and services meet the specified requirements and that all changes are properly managed.
One way of controlling a process is to use work instructions that describe step by step how certain tasks are to be carried out. These instructions can be used to train employees to ensure that they have the necessary knowledge and skills to carry out their tasks correctly. Online training can also be used to provide additional training and ensure employees are up to date with the latest procedures and requirements.
In addition to training, quality controls are an important part of process control. These reviews may include inspections, tests and audits to ensure that products and services meet the required standards. Any non-conformities or deviations from the specified requirements should be identified and rectified by corrective action.
To illustrate the importance of control in production and in the provision of services, the following table provides a summary of the most important control activities:
Control activities | Description |
Work instructions | Provide step-by-step instructions for completing tasks |
Online training | Online courses to train employees and ensure up-to-date knowledge |
Quality controls | Inspections, tests and audits to verify compliance with regulations |
Corrective measures | Dealing with non-conformities and deviations |
Documentation | Keeping records of processes and controls |
8.5.2 Identification and traceability
Identification and traceability are crucial aspects of quality control and ensuring compliance with the requirements of ISO 9001:2015. To meet customer expectations and manage operations effectively, companies must have robust systems in place to identify and track products and services throughout the process. Here are some important points to bear in mind:
- Customer communication: Effective communication with customers is essential in order to understand their specific needs and expectations. This also includes recognizing and documenting unique product or service requirements.
- Performance indicators: The introduction of performance indicators enables companies to track and monitor the effectiveness of their processes. This can help to identify areas for improvement and ensure that customer expectations are met.
- Change control: A change control process is critical for managing planned or unintended changes that may occur. This ensures that adverse effects are mitigated and that the company retains control over its processes.
- Labeling: Proper labeling of products and services is necessary to ensure traceability throughout operations. This includes labeling, marking or otherwise identifying items to ensure that they can be easily identified and tracked.
Traceability
Traceability involves keeping records or documentation that allows the company to track the movement of products or services. This can include information such as batch numbers, dates and storage locations.- Compliance with the requirements of ISO 9001:2015: The integration of identification and traceability processes into the company’s quality management system is essential in order to meet the requirements of ISO 9001:2015. In addition include documenting procedures and keeping records to demonstrate compliance.
8.5.3 Property of customers or external providers
The management of properties belonging to customers or external providers is an important aspect of effective quality control and compliance with the requirements of ISO 9001:2015. This clause, 8.4 Control of externally provided products and services, emphasizes the Company’s responsibility to ensure that property of customers or external providers is properly controlled and protected. This includes all equipment, tools or materials provided by customers or external suppliers that are used in the company’s processes.
In order to increase customer satisfaction and maintain a high level of quality, the organization must define criteria for the control of externally provided properties. This can be done by implementing procedures and work instructions that outline the requirements for the use, storage and maintenance of customers’ or external providers’ property. By clearly defining these criteria, the company can ensure that all property is managed in a manner is handled and maintained in a manner that meets the customer’s expectations and protects the property from damage or loss.
In addition, the organization must also document and record all externally provided properties in order to demonstrate compliance with the requirements of ISO 9001:2015. This documentation should include information such as the identification and traceability of the property, its condition and any maintenance or calibration work carried out on it.
8.5.4 Conservation
The maintenance of products and services is a crucial aspect of quality assurance and compliance with the requirements of ISO 9001:2015. It is important for companies to have control over the preservation of their products and services to prevent deterioration or damage that could affect their quality. This includes both the physical Preservation, such as proper storage and handling, as well as non-physical preservation, such as maintaining accurate documentation and records.
To create images in the audience’s mind, consider the following nested bulleted list:
Physical preservation
:- Proper storage conditions, such as temperature and humidity control, to prevent deterioration or spoilage.
- Appropriate packaging and handling procedures to protect products from damage during transportation or storage.
Non-physical preservation
:- Document control to ensure that the latest versions of documents are available and easily accessible to the relevant personnel.
- Keeping records for the retention of proof of conformity and for the traceability of products and services.
Effective conservation practices not only help companies to meet the requirements of ISO 9001:2015, but also contribute to overall customer satisfaction. By keeping products and services in optimal conditions, companies can ensure that customers receive high-quality, reliable and consistent products. This helps to build trust in the company’s ability to fulfill its promises.
8.5.5 Activities after delivery
Having ensured the preservation of products and services, companies must now focus on the critical post-delivery activities to maintain customer satisfaction and meet the requirements of ISO 9001:2015. These activities include actions taken by the organization after the delivery of products or services to customers. be taken. The aim is to ensure that the customer’s expectations are met and that any issues or concerns are addressed promptly and effectively.
Post-delivery activities include activities such as monitoring customer satisfaction, handling customer complaints, providing customer support and rectifying any non-conformities or defects that may occur. These activities are important for maintaining customer loyalty and trust as well as for the continuous improvement of the company’s processes and products.
To illustrate the importance of post-delivery activities, consider the following table:
Activities after delivery | Importance |
Monitoring customer satisfaction | Ensures that customers are satisfied with the products or services offered, helps to identify opportunities for improvement |
Processing customer complaints | Addresses any issues or concerns raised by customers, demonstrates the company’s commitment to customer satisfaction |
Provision of customer support | Supports customers with questions or problems, improves the overall customer experience |
Elimination of non-conformities or defects | Ensures that any issues with the products or services are resolved quickly and effectively, helps maintain product quality and customer satisfaction |
8.5.6 Checking changes
Effective change management is essential for companies to maintain control and ensure the continuous compliance of their processes and products. In the context of ISO 9001:2015 clause 8 “Operations”, the subtopic “Control of changes” focuses on the Need for organizations to take a systematic approach to managing changes to their processes and products.
To create a clear picture of this subtopic, consider the following nested bulleted list:
Changes to processes
:- Organizations must define criteria for their processes and implement control measures to ensure that these processes are carried out in accordance with the defined criteria.
- Documented information should be retained to provide assurance that processes have been carried out as planned.
- Planned changes to processes should be controlled to minimize adverse effects.
Changes to products
:- Companies must define and establish criteria for the acceptance of products and services.
- Resources should be identified and allocated to achieve compliance with product and service requirements.
- Unintended changes to products should be reviewed and appropriate action taken to mitigate adverse effects.
8.6 Release of products and services
To ensure proper approval, companies must define criteria for the acceptance and control of products and services.
Testing
Ensure that products and services meet the defined specifications through verification.
Inspection
: Conduct thorough inspections to maintain compliance with quality standards.
Validation:
Confirmation that products and services fulfill their intended purpose.
Documented information should be retained to provide assurance that approval processes have been carried out as planned. The company must retain documented information to ensure traceability to the individuals who approve the product and service release for customer delivery. In addition, it should provide documented evidence confirming conformity with the acceptance criteria.
8.7 Checking faulty outputs
Clause 8.7 of ISO 9001 describes the requirements for the control of non-conforming results within an organization’s quality management system. This clause stipulates that companies must establish and maintain procedures to remedy non-compliant products, services and processes.
8.7.1 Incorrect product or service output
The organization adheres to the following procedures:
Identification:
Quick and accurate localization of non-conformities within the plant.
Correction:
Apply the necessary corrections to address the nonconformity and prevent unintended use or delivery.
Control:
Implement appropriate measures and controls to contain and manage non-compliant output and prevent unintended use or supply.
Informing the customer
Informing the customer about non-conformities and corrective actions creates trust and enables valuable feedback that contributes to continuous improvement and increased customer satisfaction.
Continuous improvement goes beyond mere correction and segregation. It offers opportunities for growth. Analyzing non-conformities enables the identification of underlying problems and paves the way for systemic changes aimed at improving your quality management system (QMS).
8.7.2 Incorrect documentation
The organization is required to maintain documented information detailing the nonconformity, actions taken, concessions received and the person or authority responsible for making the decision on the matter.
Conclusion
Finally, section 8 of the ISO 9001:2015 standard emphasizes the importance of operational planning and control in meeting the requirements for the provision of products and services. By implementing and documenting these processes, companies can demonstrate compliance and ensure customer satisfaction.
However, some may argue that the process-oriented approach outlined in clause 8 can be time and resource intensive. Nevertheless, the benefits of improved quality, efficiency and customer confidence far outweigh the potential disadvantages.
Clause | Description | Most important measures |
8.1 Operational planning and control | Plan, implement and control processes to meet product and service requirements. Define criteria for processes and the acceptance of products and services. Identify the resources needed to comply with the requirements. Check planned changes and check the consequences of unintended changes. Ensure control over outsourced processes. | – Plan, implement and control processes to meet requirements – Establish criteria for processes and acceptance of products and services – Identify resources required for compliance – Control planned changes and review consequences – Ensure control over outsourced processes |
8.2 Determining the need for products and services | Determine the requirements for products and services. Define criteria for the acceptance of products and services. Identify the resources required to achieve compliance. Control planned changes and mitigate the adverse effects of unintended changes. Ensure control over outsourced processes. | – Identify requirements for products and services – Establish criteria for acceptance – Identify resources required for compliance – Control planned changes and mitigate adverse effects – Ensure control over outsourced processes |
8.3 Design and development of products and services | Implement the design and development process approach. Align processes with product design and development requirements. Identify key performance indicators for products and processes. Align key performance indicators with quality and business objectives. Keep documented information to create confidence in process execution. | – Implement the design and development process approach – Align processes with product design and development requirements – Identify key performance metrics – Align performance metrics with quality and business objectives – Retain documented information |
8.4 Control of externally provided products and services | Definition of control/influence requirements for outsourced processes. Evaluation of the significance/risks of outsourced activities and establishment of controls. Monitoring the effectiveness of controls for outsourced processes. The procurement, risk/compliance and operations/production functions involved. The context of the organization and the needs/expectations of the interested parties influence the control/expectations of outsourced processes. | – Define control/influence requirements for outsourced processes – Assess significance/risk and establish controls – Monitor effectiveness of controls – Involve procurement, risk/compliance and operations/production – Consider the context of the organization and the needs/expectations of interested parties |
Share this article
Written by : Jonathan
Inhalt:
Buchen Sie einen Beratungstermin
Buchen Sie einen Termin und besprechen Sie mit uns wie wir Sie bei der Zertifizierung oder andern QM-Themen unterstützen können
ISO 9001 – Leicht gemacht.
Erfahren Sie in unserem E-Book die Anforderungen der ISO 9001, die der Norm zugrundeliegenden Grundprinzipien, und den Zertifizierungsprozess
Latest articles
July 1, 2024
July 1, 2024